O Upgrade do Sistema Hidráulico do Pontoon foi realizado no canal de acesso ao estaleiro da Petromar em Ambriz.
VISÃO GERAL
O projeto de upgrade do sistema hidráulico do Pontoon começou em 2019 e comportou fases como Análise de Viabilidade, Projeto Conceitual, Projeto de Engenharia e a Construção e Montagem no primeiro trimestre do ano de 2023. A primeira etapa foi destinada ao estudo de Análise de Viabilidade, ponto que foi trabalhado de forma integrada com o cliente. O Projeto Conceitual, foi a segunda etapa e abarcou estudo dos materiais,
levantamento das necessidades do cliente, definição dos sistemas, dimensionamentos dos guinchos, bomba, motor e demais elementos, assim como a elaboração do projeto com detalhamento dos sistemas.
A etapa três correspondeu a Engenharia dos sistemas onde abrangeu o design técnico, seleção dos componentes a utilizar, fabricantes, marcas e etc.
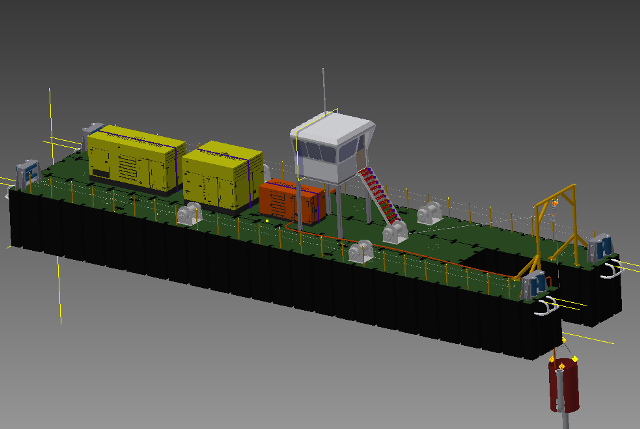
Nesta etapa foi feito um trabalho árduo integrado entre o fornecedor do material (Movicontrol) e o fabricante dos componentes (Sauer Danfoss e WEG), para este projeto foi utilizado um distribuidor da Sauer Danfoss modelo PVG 120 Proportional Valve da Serie por patentear DKMH.PK. 510.A5.02 520L0356.
Durante o primeiro trimestre do ano de 2023, a ICOS realizou a última etapa do upgrade do sistema hidráulico do pontoon de dragagem, que correspondeu a Construção e Montagem onde foram aplicados novos componentes como: HPU, Sistema de refrigeração óleo/água usando agua do mar, filtros de retorno e pressão com sensores de entupimento conectados ao controle principal e montagem das linhas do circuito hidráulico e a assemblagem de todos os componentes no local.
PROBLEMA
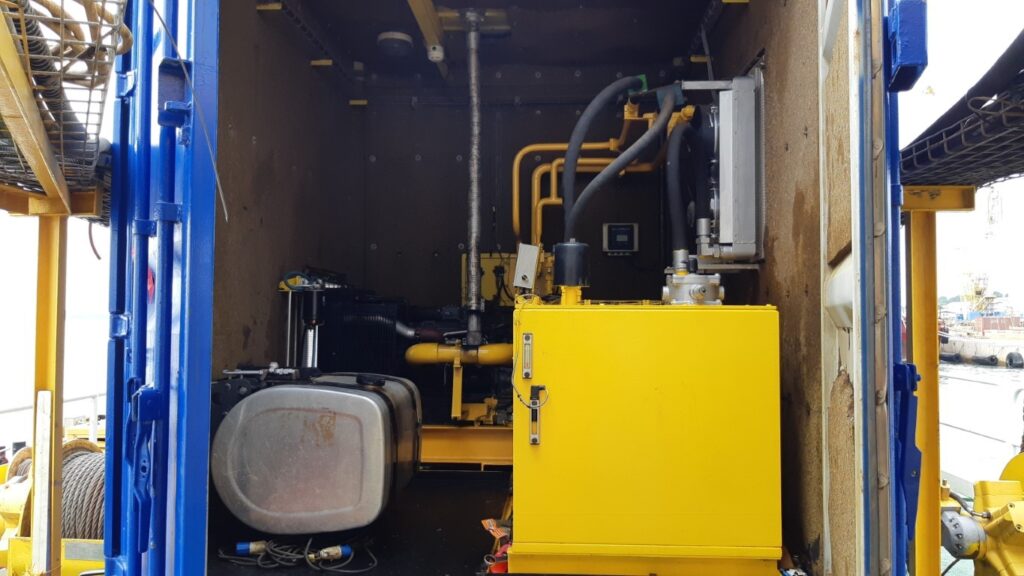
O nosso cliente já utilizava um sistema de dragagem para a limpeza de canais, porém, havia a necessidade de aumento da Segurança de Trabalho e eficiência do sistema. A segurança era um problema pois, o trabalho era realizado com as linhas de pressão exposta, ou seja, todo o circuito hidráulico passava dentro da cabine do Comandante, a uma pressão de trabalho de 200 Bar.
Já com relação a eficiência, havia um problema de consumo em potência consumida, aquecimento, bombas de caudal fixo, distribuidores antigos e pouca pressão dentro de sistema.
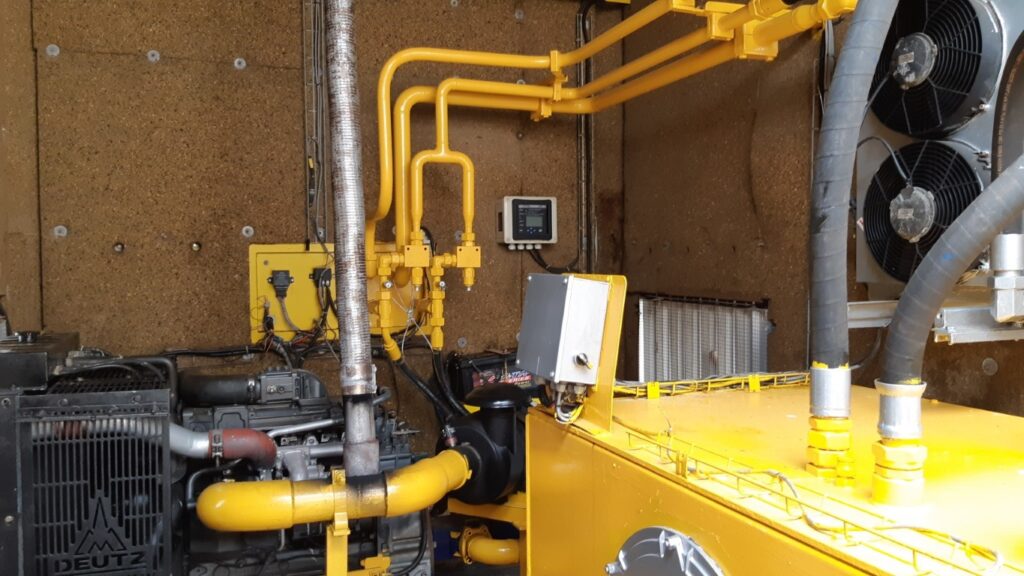
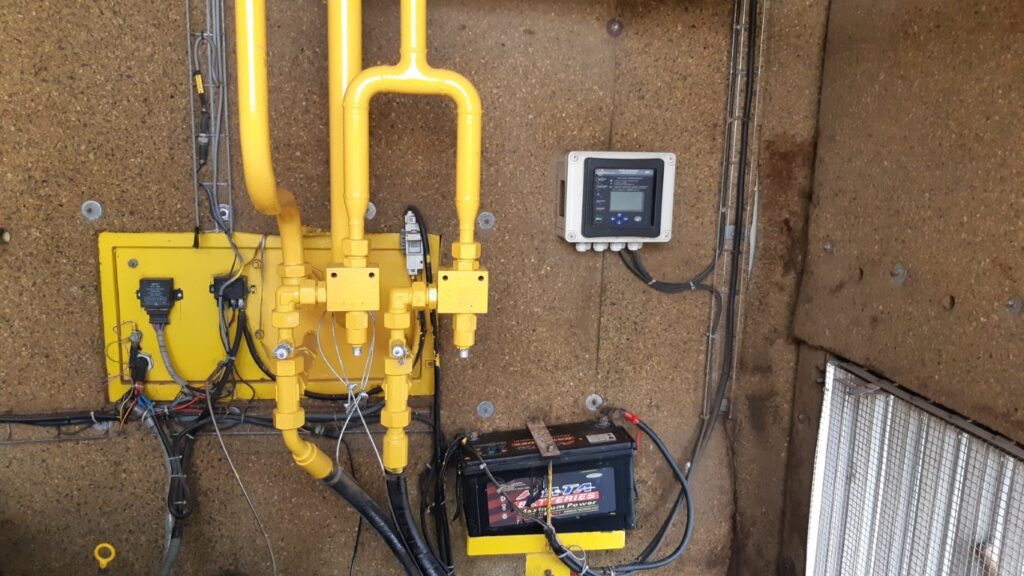
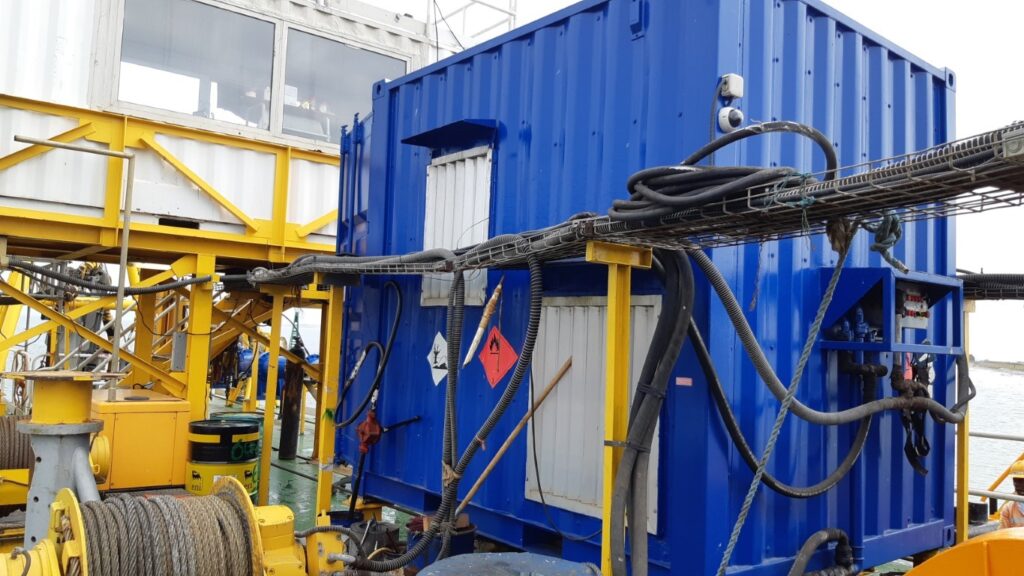
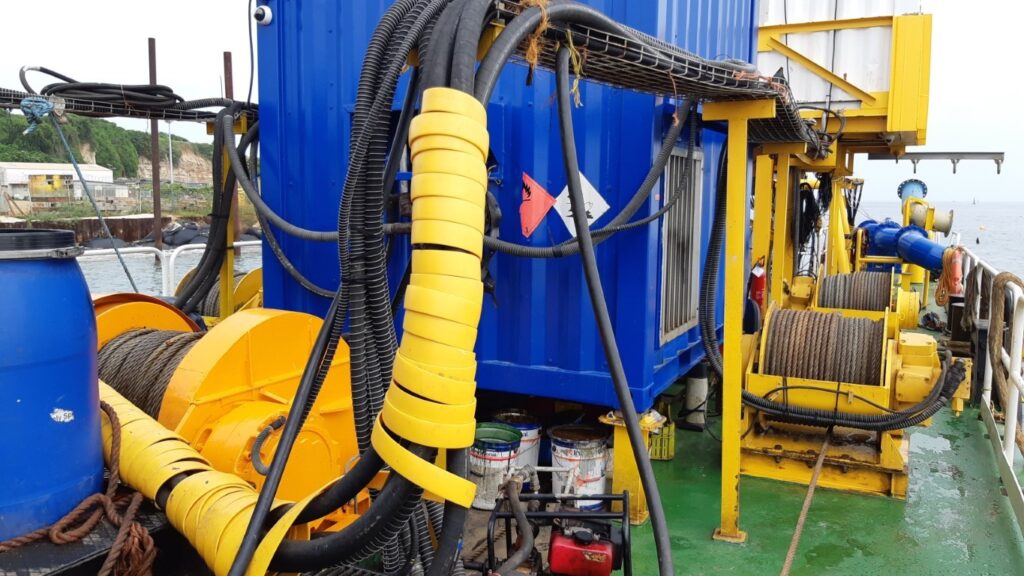
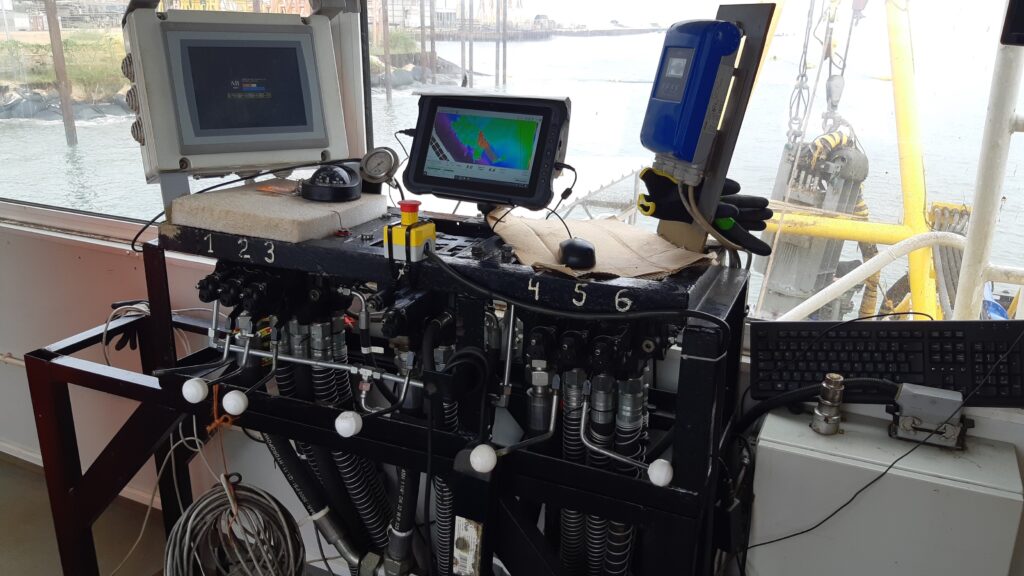
SOLUÇÃO DA ICOS
Com base nos problemas apresentados, elaborou-se um plano de trabalho integrado entre o Cliente, a ICOS (Departamento de Engenharia e hidráulica), o Fornecedor e o Fabricante. O projeto de Engenharia albergou desde a vertente sistemática, engenharia dos componentes, até as condições para obter os melhores rendimentos dentro do sistema. Deste jeito, projetou-se um Sistema novo que utiliza tecnologias mais avançada, a saber:
- A possibilidade de variação da velocidade de rotação dos guinchos a favor do distribuidor proporcional montado no sistema, permite que seja movimentado sem a necessidade de sistemas elétricos complexos, bobines ou vários distribuidores acoplados.
- Aumento do caudal em níveis necessários para levantar a bomba de sucção com um peso aproximado de 10 Ton.
- Implementação de um sistema elétrico de rádio comando com manuseio remoto, que permite ao operador a locomoção por toda a plataforma, sem a necessidade de utilização de cabos ou outros dispositivos pesados.
- Foi criada uma cabine para o capitão, com o painel de comandos simples.
- O container foi melhorado com os componentes de última tecnologia, e melhorado o layout de todos os componentes para facilitar a circulação do operador.
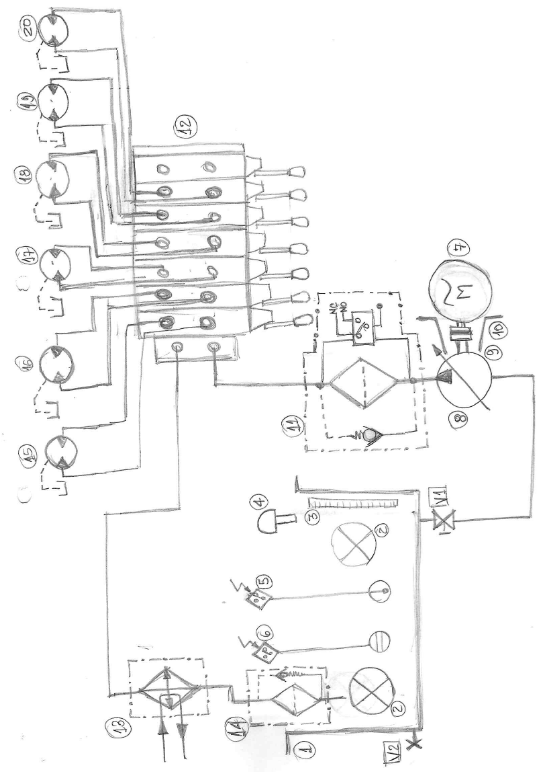
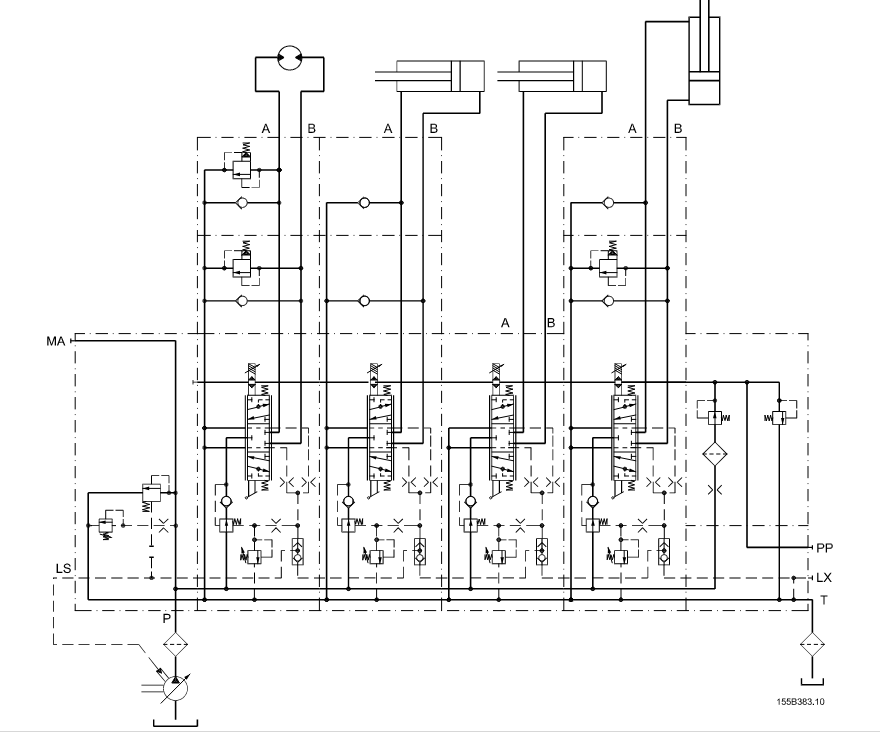
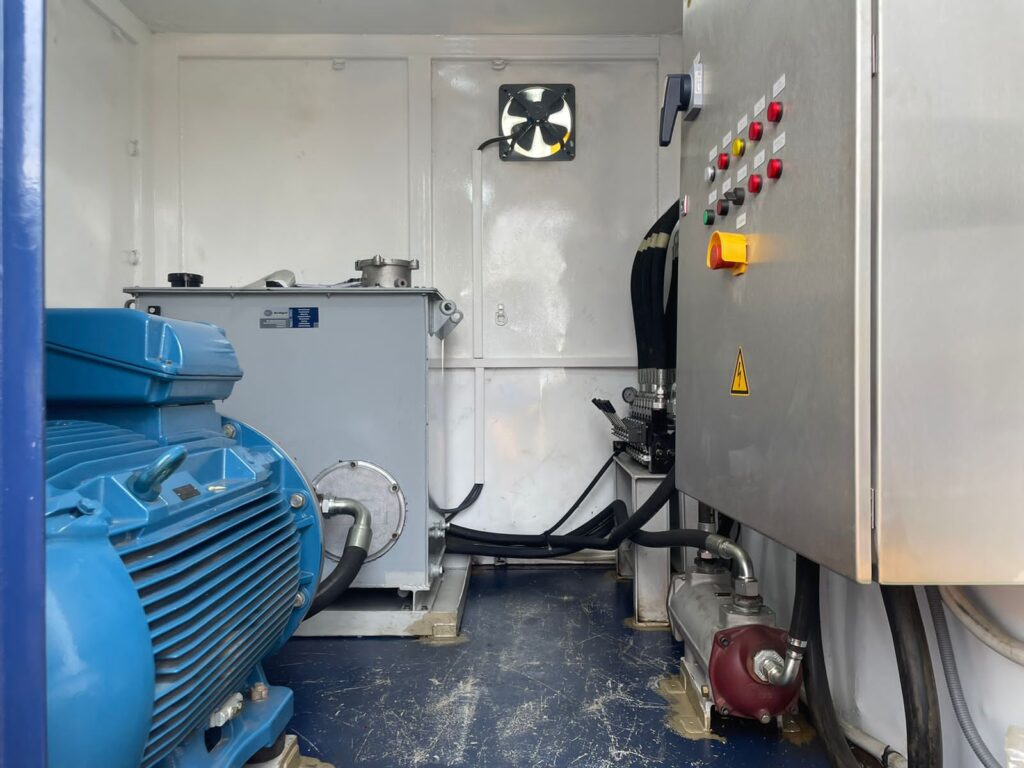
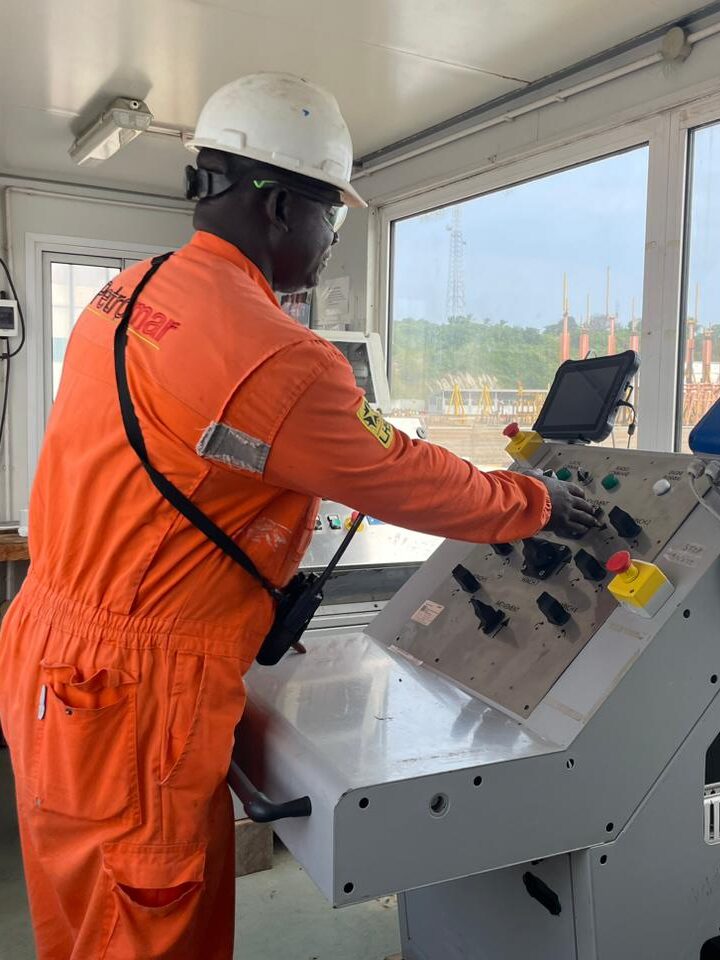
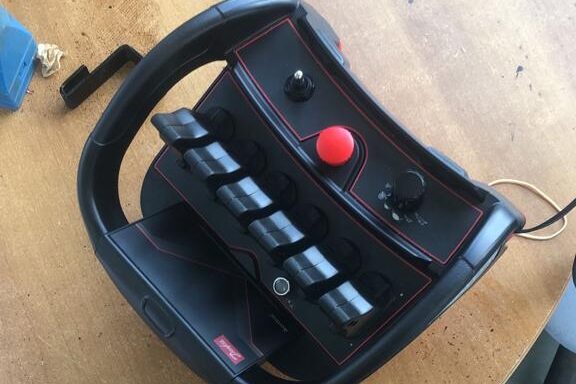
PLANO DE EXECUÇÃO
A ICOS definiu a proposta com a elaboração do escopo de trabalho, em que estava na base a disrupção do sistema existente por outro com melhor desempenho. Onde seria aproveitado o desempenho existente e incrementado novos componentes hidráulicos com a capacidade ajustada a necessidade do sistema. O desenho do cronograma do Trabalho, culminou com a montagem e teste do sistema. Abaixo, os materiais utilizados conformem a montagem:
- HPU (que incluiu conexões, mangueiras e acessórios)
- EA-137kw – 1500 RPM – Tropicalizado
- Bomba – Parker PV180 com controle binário para EA
- Válvulas de controle – Sauer PVG 120/7 – com atuadores PVM
- Filtros (filtros de retorno e de pressão)
- Opcional: Reservatório de óleo hidráulico em aço inóx com requisitos de operações marítimas,
- Indicador visual de nível, indicador elétrico de nível, indicador de temperatura (com segurança elétrica),
- Sistema de refrigeração – Trocador de calor Bowman óleo-água 67Kw de dissipação, e vazão máxima 285l/min, Bomba de água do mar para sistema e instalação conforme especificação.
- Gabinete de Controle Eletrônico/Iniciador
- Partida elétrica para EA de acordo com os requisitos do sistema hidráulico – controle de partida, controle de potência
- Caixa de controle para controle principal radioelétrico.
- Controles remotos portáteis
- Controle remoto Sauer Danfoss Portable IK4 com configuração semelhante a cabine de partida – Personalizadas de acordo com as especificações.
- Painel de controle fixo na sala de controle.
- Controle de rádio – Sauerdanfoss Ikusi – Proof1 com display TFT 3,5, rádio multibanda para comunicação Duplex. Classificação de proteção IP65/NEMA4. (inclui antenas para transmissor de rádio e recetor no gabinete de controle e HPU)
- 7 joysticks Sauer para controle independente de guinchos e função programável de guinchos múltiplos.
- Guinchos Laterais
- Guincho da bomba de areia
- Tubulação/Mangueiras Hidráulicas de Interconexão
- Tubulação rígida – Parker – aço carbono sem costura (25 mm para linhas de pressão fixadas na estrutura, linhas de retorno de 35mm) e acessórios Voss, conforme ISO 8434
- Mangueiras flexíveis – Parker ou alternativa com os mesmos requisitos de acordo com ISO 3862, fabricação, fluxo e teste de acordo com ISO 18752, API 17J/ ISO 4402, ISO4402
- Meio Hidráulico
- Óleo mineral (HLP, HVLP)
- Requisitos de segurança
- Botões de paradas de emergência no convés.
DIFICULDADES ENCONTRADAS
As principais dificuldades encontradas durante o projeto, foram as negociações devido a mudança de paradigma que estava a ser proposta, por meio de uma tecnologia disruptiva. Já com relação a aplicação a maior dificuldade esteve em conseguir os materiais, devido aos prazos de entrega por tratar-se de materiais muito específicos e não normalizados.
ANÁLISE COMPARATIVA ENTRE O SISTEMA ANTIGO E O UPGRADE
Sistema Antigo
- Ruido intenso.
- Fumo excessivo (CO2).
- Posicionamento incorreto dos componentes hidráulicos complicava a circulação do operador.
- Pouco Seguro.
- Baixa Pressão.
- Baixa Potência.
- Alto Risco de Incêndio.
- Alta temperatura
Upgrade
- Sem ruido.
- Sem fumaça.
- Maior mobilidade para o operador.
- Alta Segurança.
- Projeto realizado conforme as normas vigentes.
- Dimensionamento personalizado conforme as necessidades do cliente.
- Facilidade em Eventuais manutenções.
RESULTADOS
Ao fim de projeto foi entregue ao cliente um novo sistema com capacidade de atingir mais de 300 Bar, potências e velocidades duplicadas. Em que é garantida a segurança do comandante por meio da concentração da pressão dentro do contentor fora da cabine. A capacidade foi aumentada com conversores de caudal variável, arrancadores automáticos que possibilitam ao cliente gerir a potência e a eficiência, para pressões muito mais elevadas com a mesma potência dos guinchos. Assim como, a entrega de toda a documentação técnica desde Relatório do comissionamento do sistema hidráulico, diagramas e respetivas listas de peças hidráulicas e elétrica e o Manual de operações com instruções de manutenção.
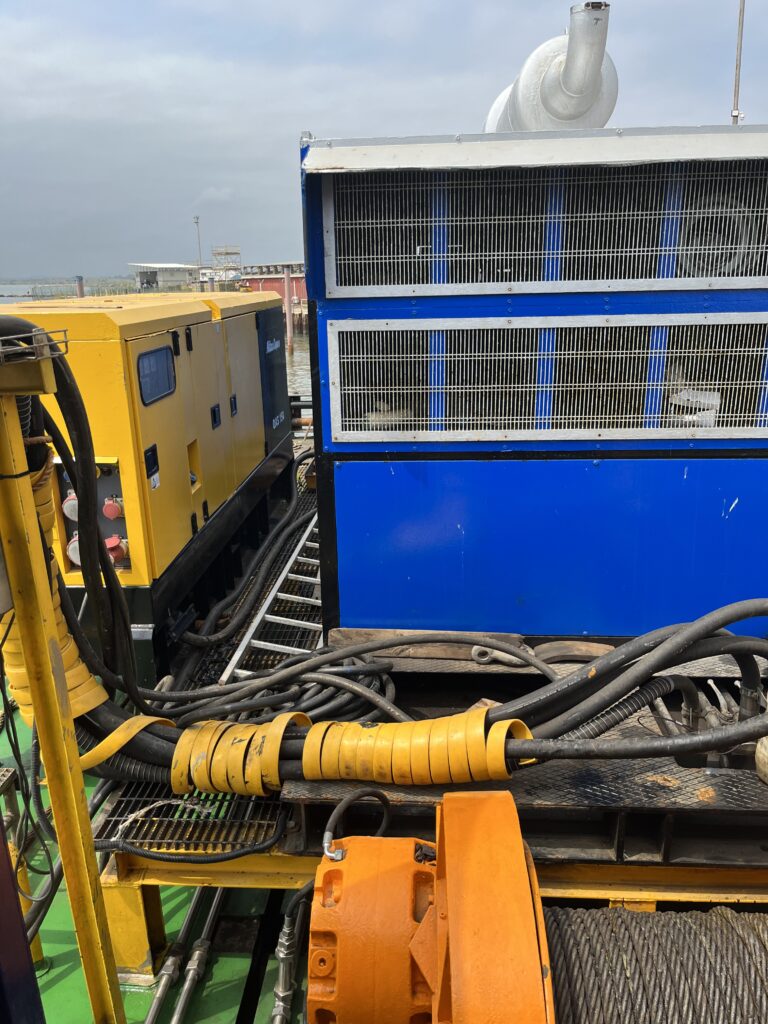
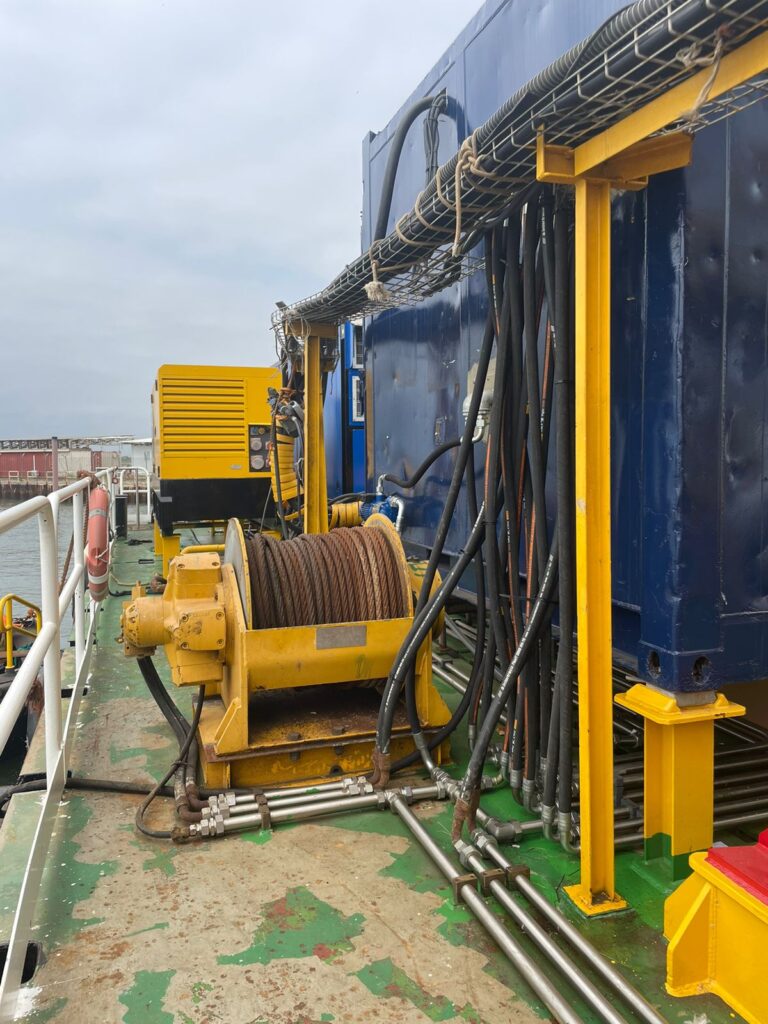
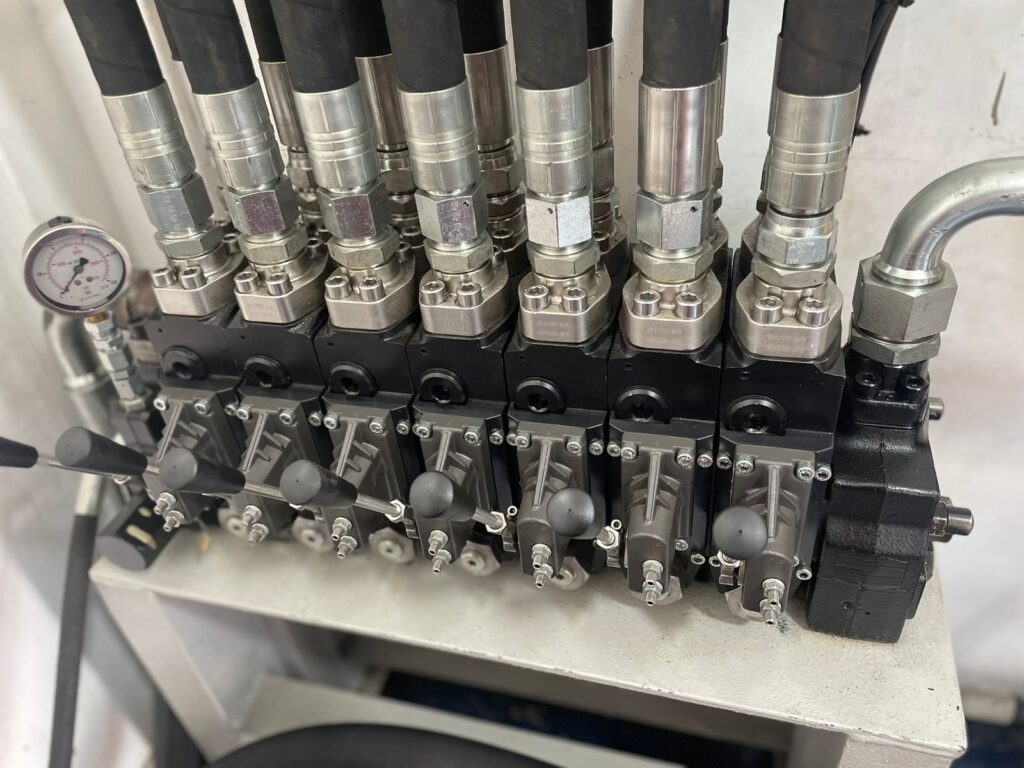
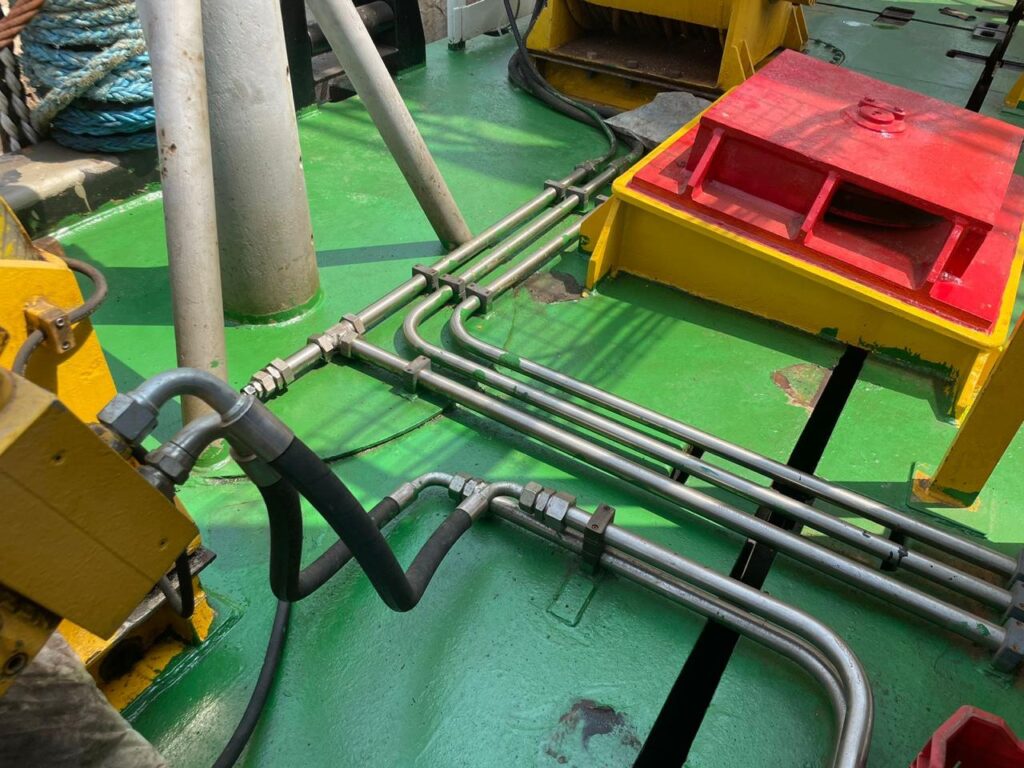